The MEP industry is constantly evolving.
We share our perspectives and insights here on key trends and issues related to our work.

Our Team’s Deep Hospital Expertise Continues to Expand
At Certus we design solutions for complex healthcare projects. Having completed over 400 projects over the past five years, we’ve selected five key project types that showcase our expertise, delivered in close collaboration with our valued clients and partners.

Certus Celebrates Five Years of Partnership and Growth
Founders Danna Jensen, Kevin Miller, and Roger Koppenheffer founded the company in 2019 with a vision to create a firm that could provide clients and partners with a dynamic, responsive, and innovative solutions team to meet their healthcare MEP needs.
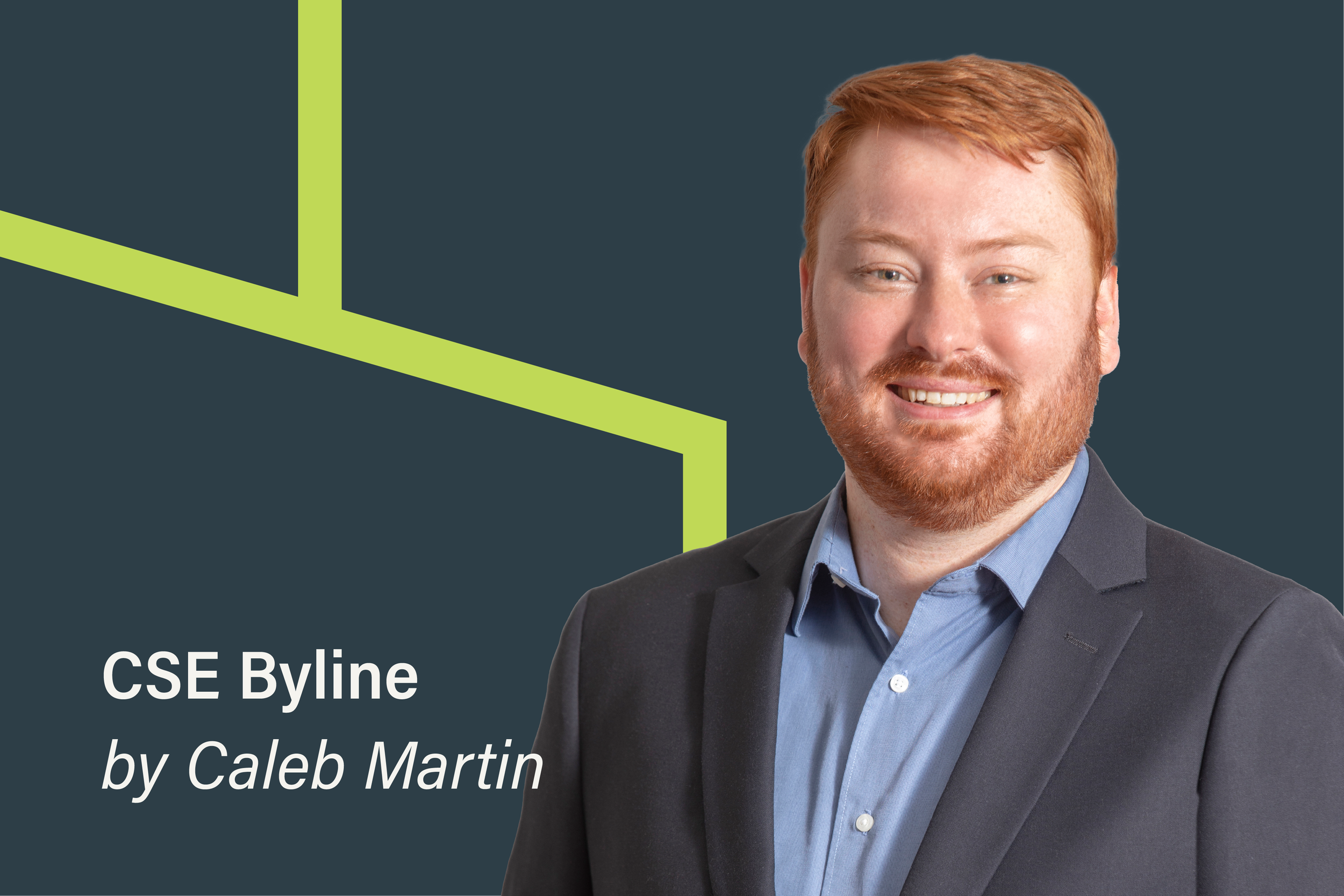
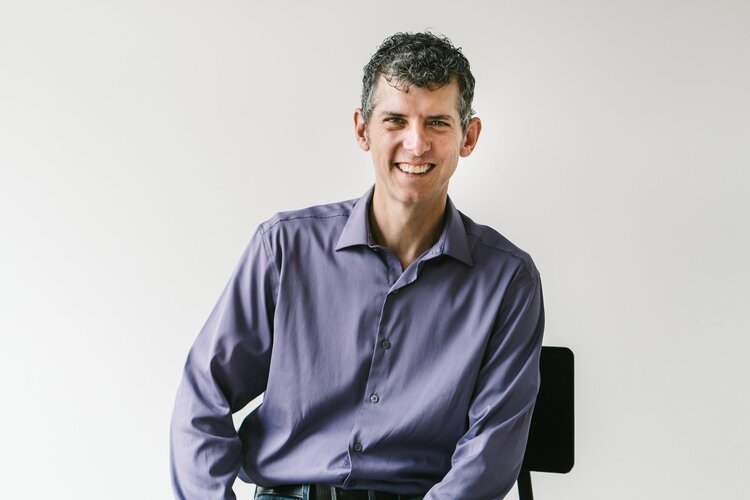
MEP Round Table by CSE Magazine: How pandemics affect building design
COVID-19 affected engineers and building professionals’ designs in many ways. Consulting-Specifying Engineer hosted an MEP Round Table to discuss how the pandemic affects building design. Kevin Miller provided valuable insight on the topic as a member of this round table.

Critical Power: How to specify backup, standby and emergency power in mission critical facilities
When designing backup, standby and emergency power systems for mission critical facilities, there are several considerations beyond NFPA 70: National Electrical Code and other building code requirements that must be addressed.
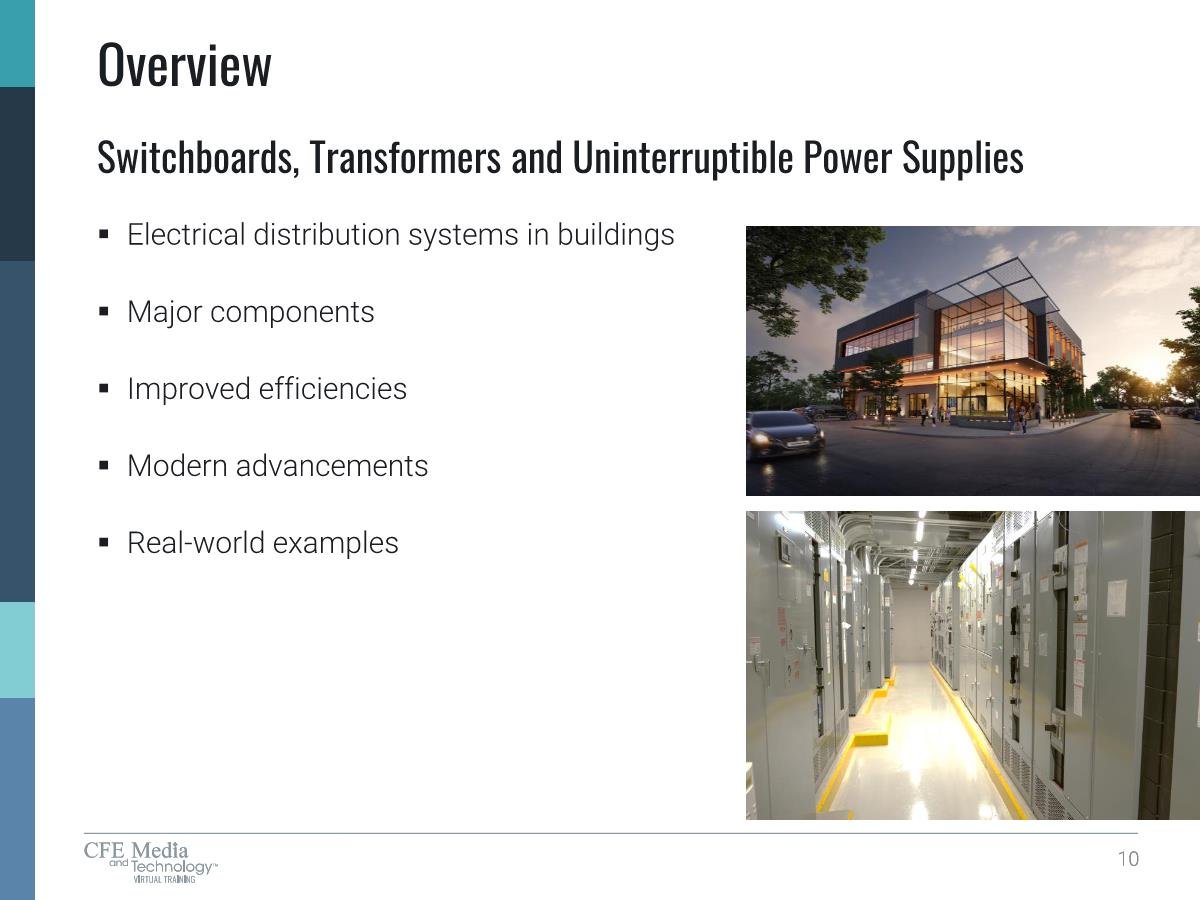
Webinar: Critical Power: Transformers, uninterruptible power supplies and switchgear
Engineers should know the design concepts for selecting and sizing transformers, uninterruptible power supplies and switchgear to help achieve energy efficiency in various facilities, including data centers, hospitals and other buildings that require this equipment.
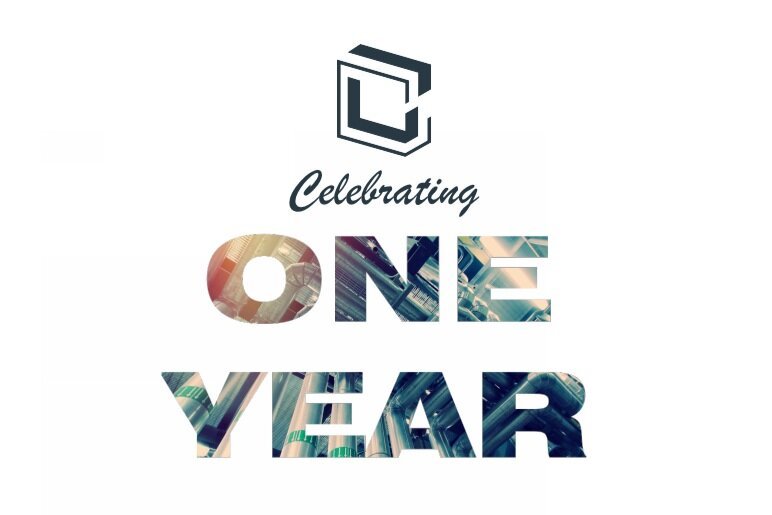
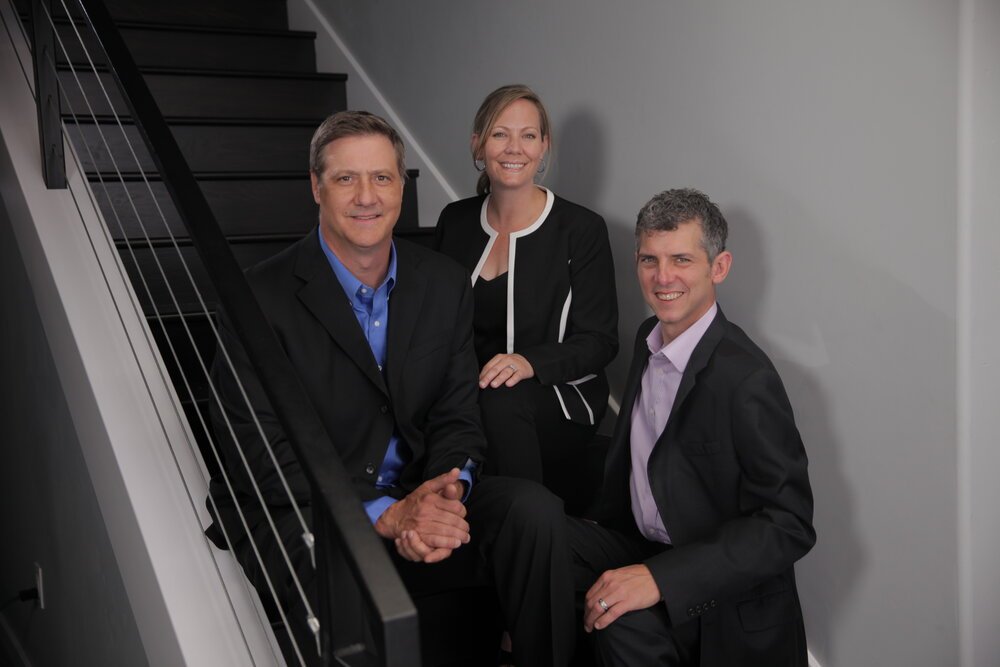
COVID-19 Q&A: Certus experts discuss health care business trends
To learn more about how consulting engineers are working, Consulting-Specifying Engineer discussed the COVID-19 crisis virtually with three experts from Certus. Both business and engineering trends were discussed in depth.
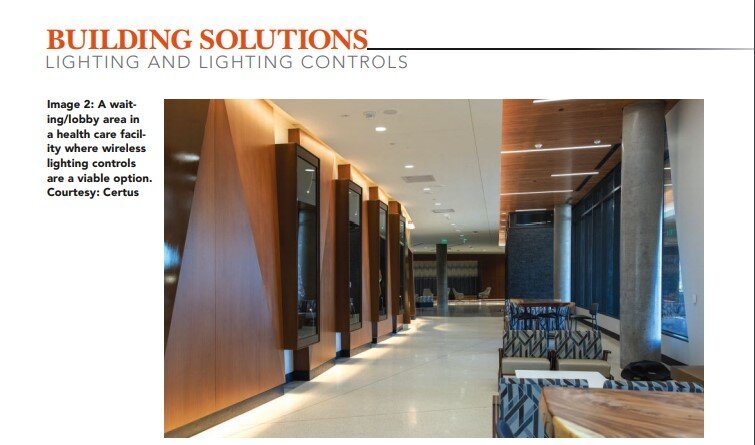
Future-Proof Health Care Facilities With Wireless Lighting Controls
As the industry continues to gain momentum in wireless control solutions, what is the future of lighting controls in critical applications such as a health care environment?
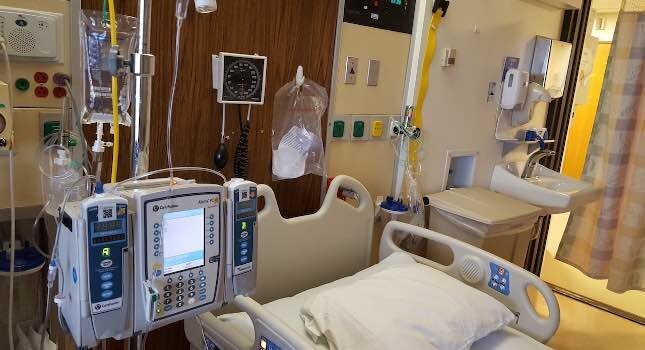
Your Questions Answered: How to specify backup, standby and emergency power in mission critical facilities
Electrical engineers must understand the specific owner project requirements for the building’s power systems and ensure that the generator specification and system topologies meet all those requirements for cost, construction schedule, component performance and system maintainability.